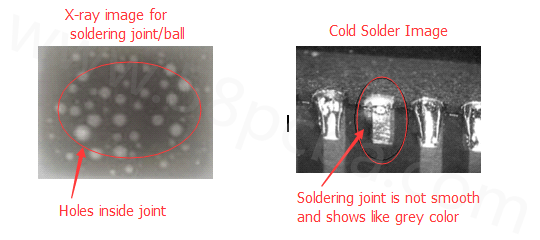
Analysis of Root Causes
▪ Too much flux is applied in the solder paste. The flux doesn’t have sufficient time to outgas before the solder has transitioned to a solid state.
▪ The preheat temperature is too low so any solvent in the flux is difficult to vapour out completely.
▪ The soak zone time is too short during the reflow process.
▪ Lead-free solder typically has a 4% shirinkage in volume when it is cooled down to a solid state. It is possible to obtain voids when large pads are cooled down unevenly.
▪ Paste oxidation occurs.
Corrective Actions
▪ Reduce the amount of solder paste deposited.
▪ For large pads, use small opening grids instead of a large aperture.
▪ Extend the preheat time so it is long enough.
▪ Extend the soak zone time so it is long enough.
▪ Always consider new solder paste for BGA assembly.
While a normal solder joint is usually bright and shiny, a cold Solder joint is an abnormally dull, non-reflective, rough surface on the solder joint.
Analysis of Root Causes
▪ The pre-heat time is too long and too high, preventing the flux from activating.
▪ The solder paste has expired.
▪ There is not enough heat absorbed by the solder.
▪ The cooling speed is too slow.
Corrective Action
▪ Adjust the reflow profile according to the manufacturer’s specification.
▪ Ensure the peak temperature is at least 15°C above the solder’s melting point for more than 45 seconds.
▪ Change to a new type of solder paste.